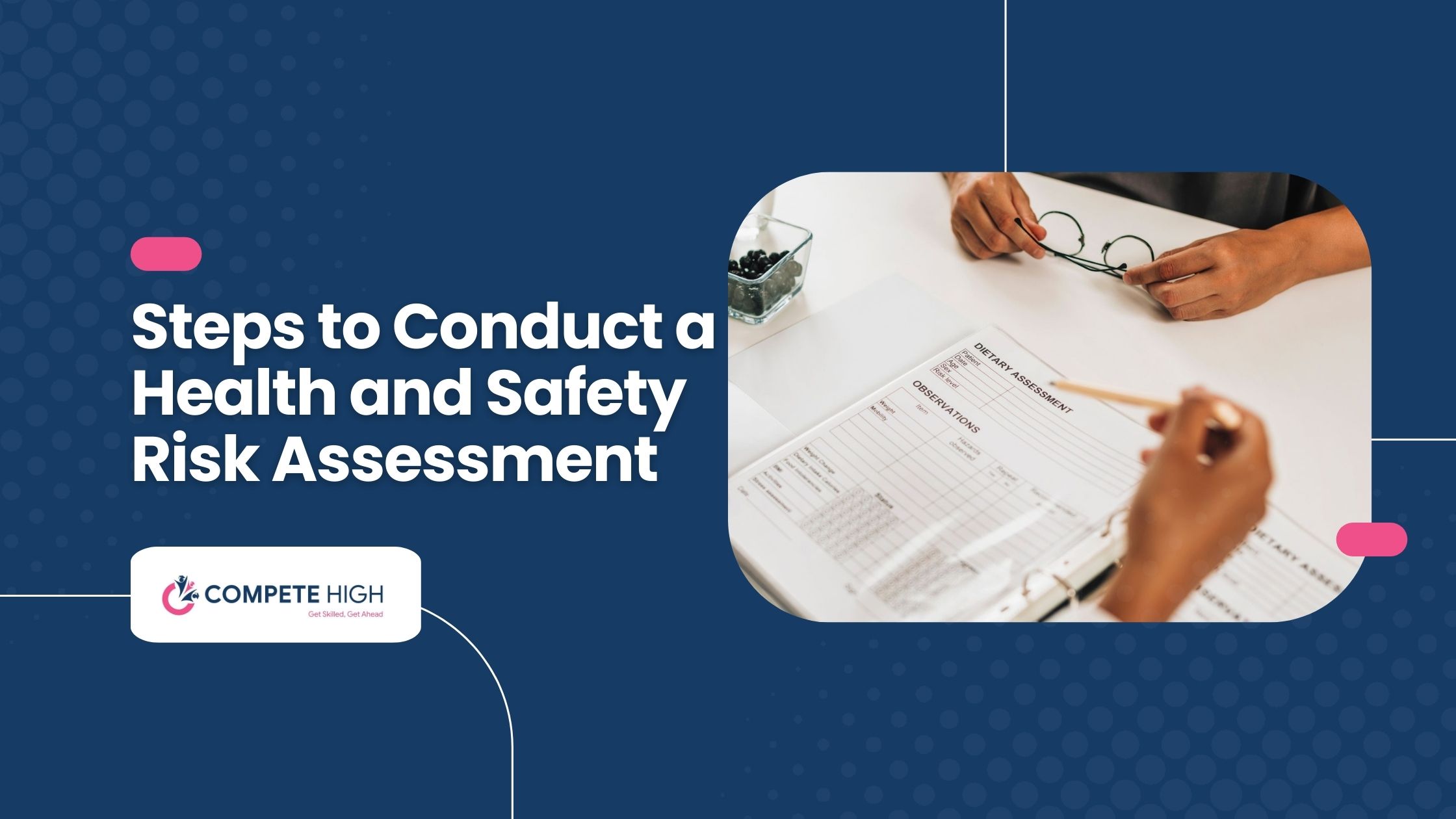
Health and safety at work are an imperative. It ensures the well-being of employees and a favourable atmosphere for accomplishing organisational goals. Health and safety issues are incorporated throughout the whole business. One of the most important methods to ensure a safe and healthy working environment is to conduct health and safety risk assessments.
In this blog, I will explore the steps to a successful health and safety risk evaluation. It will guide a business to identify risk hazards, estimate risks, and choose appropriate control measures.
Overall, health and safety risk evaluation is crucial to protecting people and businesses.
Understanding Health and Safety Risk Assessments
Definition and Importance
What Is a Health and Safety Risk Assessment? A health and safety risk assessment can be defined as ‘the process of evaluating the potential risks associated with hazards in the workplace.’ Health and safety risk assessment comprises identifying hazards (or potential hazards), assessing the risk associated with the hazard, and determining either measures to control or avoid the risk entirely. Those involved in evaluating health and safety risk need to answer three simple questions: what could go wrong, how likely is it that it will go wrong, and what are the consequences should it do so?
For example, health and safety risk evaluation are conducted for workplace hazards, including physical, chemical, biological, and ergonomic health and safety risks. By identifying potential risks, businesses can proactively mitigate any threats to their team members’ wellness and the state of company resources.
How regularly health and safety risk assessments in the workplace will keep the workplace safe: It is important to conduct health and safety risk assessments because they offer an opportunity to figure out potential dangers in the workplace before people are injured by them. Furthermore, this action helps to reduce the number of dangerous cases, which, obviously, results in less money spent on a definite claim.
Regular risk assessments help to demonstrate a company’s concern for employees’ health and safety. Knowing that one’s workplace is being closely monitored can help support employee morale and productivity.
Health and safety risk evaluation can also help businesses anticipate threats, giving them an early warning system to deal with issues before they materialise. The vigilance of this type will help to keep the workplace safe and effective.
Legal and Regulatory Requirements
To summarise the legal requirements for risk assessment, many countries have specific laws and regulations that require health and safety risk assessments. In the UK, for example, it is illegal to be an employer without considering health and safety, and the Health and Safety at Work Act 1974 stipulates that employers must conduct regular risk assessments to ensure the well-being of their staff.
Not adhering to such rules exposes the company to serious penalties, such as fines and even lawsuits. This is why any business should maintain a great level of sense regarding these legal requirements.
Appreciation of the necessity of adhering to health and safety: It is clear that compliance, not only when it comes to health and safety but also in a more general sense, is very important. Failure to do so can lead to legal repercussions and is thus an important factor to consider here.
Compliance can prove to regulators, shareholders, and customers that the company takes the issue of safety and legality seriously and can therefore earn the company a stronger reputation and the trust of its employees and customers.
Workers undergo regular risk assessments from time to time to make sure they are complying with the current health and safety standards. This means they can show any inspectorate that they are actively applying existing laws, rules, and regulations.
Preparing for the Risk Assessment
Gathering Information
Establish Hazards and Risks: The first step in a health and safety risk assessment is to identify potential workplace hazards. Hazards can be physical, chemical, biological, ergonomic, etc. Consider everything in the workplace: equipment, processes, and materials.
Draw up a list of all the identified hazards. This will be your starting point for the health and safety risk evaluation process. Consider both obvious and less-obvious hazards.
Talk to employees and review your past incident history. Employees live in the workplace every day and are aware of many of the hazards and hazardous conditions that supervisors and managers may overlook. Talk with employees to obtain their perspective about the work environment, issues of concern, and hazardous behaviours they have seen.
Looking back at previous accidents, near-misses, and accident reports can also help identify repeating issues and causes for more attention. Learning how others dealt with the problem can help with prevention and mitigation.
Selecting the Assessment Team
Appoint Skilful Members for the Assessment Team: Essentially, the kind of team you can assemble and experience will determine how well you can accomplish the health and safety risk assessment and how productive your subsequent control actions will be.
Choose team members from different parts of the company to ensure a broad-risk evaluation. This approach will achieve a more sound evaluation that is not contaminated by parochial thinking.
Roles and Responsibilities: The roles and responsibilities for the performance of each health and safety risk assessment team must be clearly defined. Participants must be assigned the relevant tasks. A team must be more than the sum of its parts for a health and safety issue. Task allocation can ensure process efficiencies, such as allowing the person with the highest expertise to identify hazards or the most relevant person to score a risk.
The team will have a team leader who is in charge of assessment. The team leader prepares an assessment plan and ensures the tasks are completed on time while the final report is thoroughly prepared.
Regular update meetings should be scheduled to consider the findings, share personal insights, and ensure everyone is on the same wavelength. Without adequate communication and collaboration, a thorough risk assessment would not be realised.
Identifying Hazards
Types of Hazards
Physical Hazards: Physical hazards are common in the workplace. They include injuries from machinery with moving parts, from slipping and tripping on wet or uneven surfaces, and from working at heights. Machinery should be guarded, and floors should be kept clean and dry. Chemical Hazards: Exposure to chemical hazards can occur through inhalation, ingestion, or skin contact with harmful substances. Engineers often design the containment, extraction, or monitoring of these hazards.
Another type of physical hazard is noise, which causes hearing loss over time. Protective gear and noise-eliminating technologies should be employed in noisy workspaces.
Chemical Hazards: Chemical hazards can originate from exposure to harmful substances, such as gases, liquids, and solids, that are toxic, corrosive, or flammable. Care must be taken to store, label, and use chemicals safely.
It is essential to vent the area when handling volatile chemicals to avoid inhaling toxic fumes. Employees must be trained about the safe handling of chemicals and the use of PPE.
Biological Hazards: These refer to pathogens such as bacteria, viruses, fungi, or other microorganisms that cause human illness and which occur in medical settings, labs, and in particular in places with poor sanitation practices. Good hygiene practices (e.g., cleaning up after illnesses, avoiding contact with potentially infectious people, not sharing food or cutlery with them, thorough decontamination of lab equipment, etc.) and vaccination programmes play a fundamental role in mitigating risks.
Biological safety risks can also arise from the handling of animal tissues, such as mould and mildew. All these risks dictate cleaning and disinfecting procedures.
Ergonomic Hazards: Hazards related to the design of the workplace and tasks and can cause injuries (e.g., musculoskeletal) from repetitive movements, poor lifting or repositioning techniques, or poor design of workstations. Workstation design and training on proper body mechanics can minimise these risks.
Using adjustable furniture and equipment can help staff maintain good posture and prevent injury. Allowing staff to have breaks and altering the job they are doing can prevent repetitive strain injuries.
Methods for Identifying Hazards
Regular Workplace Inspections: Regularly inspecting the workplace is the best proactive measure. Employees can take safety walk-throughs if they have been trained in them. Several safety officers can do regular rounds and inspect the workspaces. Also, the whole work environment can be inspected by creating formal checklists, covering all areas.
The inspection should include all premises, including parts of the workplace that are not often accessed, with the identification of hazards and their remediation before any accidents happen.
Employee Surveys and Feedback: Employees are often the first to recognise hazards that might be overlooked by management. Regular surveys and the gathering of feedback about safety concerns are therefore essential. Developing an organisational culture where such feedback is expected and encouraged is of paramount importance.
Periodic safety meetings where employees can express their concerns and share ideas help improve overall safety as well. By making everyone part of the solution, all hazards get addressed.
Reviewing Accident and Incident Reports: Look back at accident and incident reports to identify common hazards and things that should be updated. Look for trends in the data to identify common causes of accidents and prevent them in the future.
Keeping a detailed record of all incidents, including near misses, can help trace out the image of a safe working place and analyse the past again and again to improve safety measures.
Assessing Risks
Evaluating the Likelihood and Severity
Determining the Likeliness of Each Hazard Occurring: Once hazards are determined, the next step is to determine the likelihood of these hazards occurring. This would mean considering how often that hazard is present while accounting for the conditions in which there is a potential for an incident. A hazard that is constantly present, say wet floors in a kitchen, might have a higher likelihood than a piece of equipment that is rarely used.
Historical data from previous incidents, for example, can serve this purpose. A likelihood assessment can also be aided by employee feedback and expert judgement, such as that of a health and safety officer.
Evaluating the Potential Severity of Each Hazard: The severity level of a hazard is a measure of the potential risk if the hazard occurs. This takes into account the possible injuries, health effects, and extent of property or environmental damage an event may bring. High-severity hazards can involve serious injury or even death.
Think about both short-term and long-term effects. It might be clear that exposure to a chemical is burn-inducing, but if the same chemical has not been shown to have long-term effects like cancer, you will not be able to accurately report the risk.
By multiplying the probability and the severity, numerical factors about the expected consequences of each hazard are combined into an indication of the overall risk. This is fundamental to decisions about which hazards require the most urgent attention.
Risk Rating Systems
Assessing Hazards with a Risk Matrix: A risk matrix can help select hazards with a high probability and severity. A risk matrix graph has two axes: one is the likelihood of an incident, while another is its severity, with green near the bottom and red near the top. Each hazard is plotted on the risk matrix diagram. For example, a braking system hazard has a moderate likelihood and moderate severity, while a skylight could break with a high likelihood and low severity. The size of the risk matrix area can help you prioritise hazards.
For example, a hazard with high likelihood and high severity will be in the top right corner of the matrix and require urgent control measures. A hazard with low likelihood and low severity will be in the bottom left corner and require a lower priority.
The risk matrix can help you decide where to invest resources and work towards mitigating risks, and it lets you see at a glance how hazards rank.
Example of risk rating systems: Numerous risk rating systems could be developed within the organisation based on its needs and ultimate goal. A simple system is to assign a likelihood score and a severity score for each hazard, then multiply these scores together to get a final risk rating. For instance, if likelihood is assessed on a 1–5 scale and severity on a scale of 1–5, a hazard with a likelihood score of 4 and a severity score of 5 would have a risk rating of 20.
A second method is the Traffic Light System, which refers to risk as red (high risk), yellow (medium risk), or green (low risk). The colour code is easily recognisable and easily communicated across the organisation.
There is, however, no perfect risk rating system—a fact that you’ll hope your company always recognises. When you’re in a newsroom full of 20-somethings, you might not need as much complexity as between a dumper and an excavator on a construction site or jet fuel versus saline in an airport. The more complex your workplace and the more varied the risks within it, the more care and thought you should put into the system of assessing and prioritising risk.
Implementing Control Measures
Hierarchy of Controls
Elimination: One of the best precautions for controlling hazards is to get rid of them. If you don’t need something, removing it can eliminate the hazard. For example, eliminating the need for workers to perform a risky process by automating the process can eliminate the hazard.
Substitution: Another possibility is to substitute one thing for another. If elimination is not an option, then substitution can be used by replacing a hazardous substance or process with another, less hazardous substance or process. For example, if bleach is being used for laundry, it could be substituted with vinegar, which is nontoxic but still effectively cleans clothes.
Engineering Controls: Whereas elimination and substitution are the preferable options when possible, engineering controls are the next best option after elimination and substitution. Engineering controls involve making physical alterations to the work environment that reduce the risk of exposure to workplace hazards. For example, installing ventilation systems to remove contaminants from the air or installing guards on machinery to prevent human injuries.
Effective engineering control does not rely on human action. Once put in place, these controls reliably shield workers from hazards.
Administrative Controls: Administrative controls are organisational interventions that change procedural or policy practices, including job rotation to decrease exposure to repetitive-strain injuries, scheduling breaks to prevent fatigue, and providing training in safe work practices.
Administrative controls are important but less fail-safe than engineering controls because their effectiveness depends on workers following procedures each time the control is in place, and regular training and reinforcement are required.
Personal Protective Equipment (PPE): PPE is the least preferred form of control because it relies on personal behaviour. It includes earplugs for workers near loud machines, gloves to protect against cuts and abrasions, safety goggles to protect against eye injuries, or respirators to protect against dust, vapours, or welding fumes, among many other examples.
It is also important to provide employees with training on how to wear PPE properly and to inspect and replace all equipment at regular intervals to ensure continued protection.
Developing an Action Plan
Prioritising According to Risk Level: Once control measures have been identified, they need to be prioritised according to risk level. High-risk hazards pose a greater threat to safety and therefore should be tackled first. Use the risk matrix developed in the previous steps to help with prioritisation.
You can do the most good by honing in on the biggest threats to worker safety first.
Assign responsibilities and timelines for implementing controls. Create an action plan detailing the tasks involved in implementing each control measure, who is responsible for them, and by when. Identify what needs to be done, who will do it, and when.
Draw up workable timescales for controls, taking into account the resources and time that are needed. Review progress and adapt the plan as necessary so that it remains on track.
Crystallisation is best achieved through effective communications so that everyone in the organisation is clear about who is doing what and why they are doing it. Collective ownership of and commitment to controls can be enhanced by offering ongoing support and resource reviews that help to maintain momentum and embed the controls within day-to-day working practices.
Documenting the Risk Assessment
Creating the Risk Assessment Report
Components of a Comprehensive Risk Assessment Report: A health and safety risk assessment report should begin with an introduction that explains the purpose and scope of the analysis. Some components of this report could include the team who performed the assessment, methods of identifying hazards, and methods for evaluating risk.
Identify the hazards and risks, record the results of any health and safety risk assessment undertaken, the control measures introduced or planned, the dates on which action will be taken, and who is responsible. And then come the summary and recommendations for improvements and further actions.
Give each section a title so that the reader can navigate through the report easily. Use material such as charts and tables to provide detailed information, and present your conclusions and key findings with clarity.
Significance of Clear and Quality Documentation: Clear and quality documentation is important to capture the findings of health and safety risk assessment and control measures undertaken by following occupational hygienists; as a result, it can be used for further information and evaluation. Moreover, a clear description of health and safety risk assessment and its performed analyses can help everyone working on related projects comprehend the identified risks and control measures.
Using this information effectively facilitates clear reporting of the results, making it easier for workers and stakeholders to understand how the risks should be prevented or mitigated. Further to this, maintaining clear documentation of findings ensures compliance with legislation and regulation, providing auditable evidence that health and safety risks are being effectively managed.
Communicating Findings
Communicating the Outcomes of the Risk Assessment with the Employees: Once the health and safety risk assessment is complete, it should be communicated to all the employees, as this helps them understand the hazards found and the control measures put in place to minimise the risks. Convene a meeting or a briefing session to present the key points of the health and safety risk assessment, looking into the most significant risks and the control measures in place.
Make the full health and safety risk assessment report available to workers in print or electronic form, and invite them to review that report and ask questions if they need any clarification. The goal here is to create a safety culture wherein workers feel free to ask questions and can see for themselves how they can contribute to safety every day.
Training Staff on New Safety Procedures: Implementing new safety procedures generally means you have to provide additional staff training. Design a training session that involves explaining the new procedures, describing why they’re important, and how they’ll be rolled out. It would be great if the session incorporated diverse learning styles, which can be accomplished by providing different materials such as presentations, hands-on demonstrations, or written resources.
Ensure employees have regular training and schedule follow-up training sessions for new hires to help each stay safe. When something goes wrong, take time to talk through the issues with employees and ensure that everyone has the resources and skills to follow safety protocols. Make sure that training isn’t a one-time event but a continuous commitment throughout their time in the workplace. Consider consistently offering safety manuals and refresher courses to help maintain high workplace standards of safety.
Monitoring and Reviewing
Regular Monitoring
Regular checks to ensure controls are maintained. Once the controls have been established, they still need to be monitored periodically to ensure that they function as intended. Create a schedule for regular checks of controls to verify that they are effective. For instance, it could involve performing routine checks on equipment, processes, and work areas to review the calibration of safety procedures.
Monitoring should be systematic, covering all aspects of the health and safety risk assessment: for instance, is the safety guard on the press back in place, are staff wearing personal protective equipment (PPE) correctly, and are administrative controls such as training and procedures being followed?
Keeping a Log of Monitoring Activities: Record all monitoring activities to maintain information on current and ongoing compliance and effectiveness. The record should include the dates of inspection, the nature of the findings, the actions taken to correct or address the issues, and what follow-up activities took place. Keeping a log will help keep track of the effectiveness of all of the control measures over time and also provide proof of your best efforts at safety.
These records can help pinpoint trends and areas for improvement. By reviewing monitoring logs regularly, discrepancies can be identified to take corrective action.
Reviewing and Updating the Assessment
Revisit the Risk Assessment Periodically: Conducting the health and safety risk assessment is just the beginning. It’s important to revisit it periodically to ensure that you’re keeping it current. Schedule periodic reviews, such as annually or biannually, to check the list of hazards regularly and determine whether the controls currently in place remain adequate.
That helps to make sure the heath and safety risk assessment is still current, as the risk may change over time, and it also allows the assessment to identify whether any new hazards were not present when the assessment was originally completed.
Revising the Assessment in Response to Change in the Workplace or Incident: The workplace changes quickly; new equipment, processes, or personnel can alter existing hazards. Revise the health and safety risk assessment when major changes occur so that all workplace hazards are identified.
Furthermore, if there is a minor incident or near-miss, update the risk assessment to prevent a recurrence. Investigate the minor incident in rigorous detail, including identifying the root cause and amending, calling for a review, or devising further control measures. This is a proactive approach that ensures the institution’s working environment remains safe and can help prevent the occurrence of similar incidents in the future.
Conclusion
Therefore, we have provided you with factors to consider when conducting a health and safety risk assessment in this blog. They include steps to take such as: understanding the process; preparing; identifying hazards; assessing risks; introducing control measures; documenting the outcome; and regularly monitoring and reviewing the assessment.
Keep your team safe via health and safety risk assessments. Want to know more?