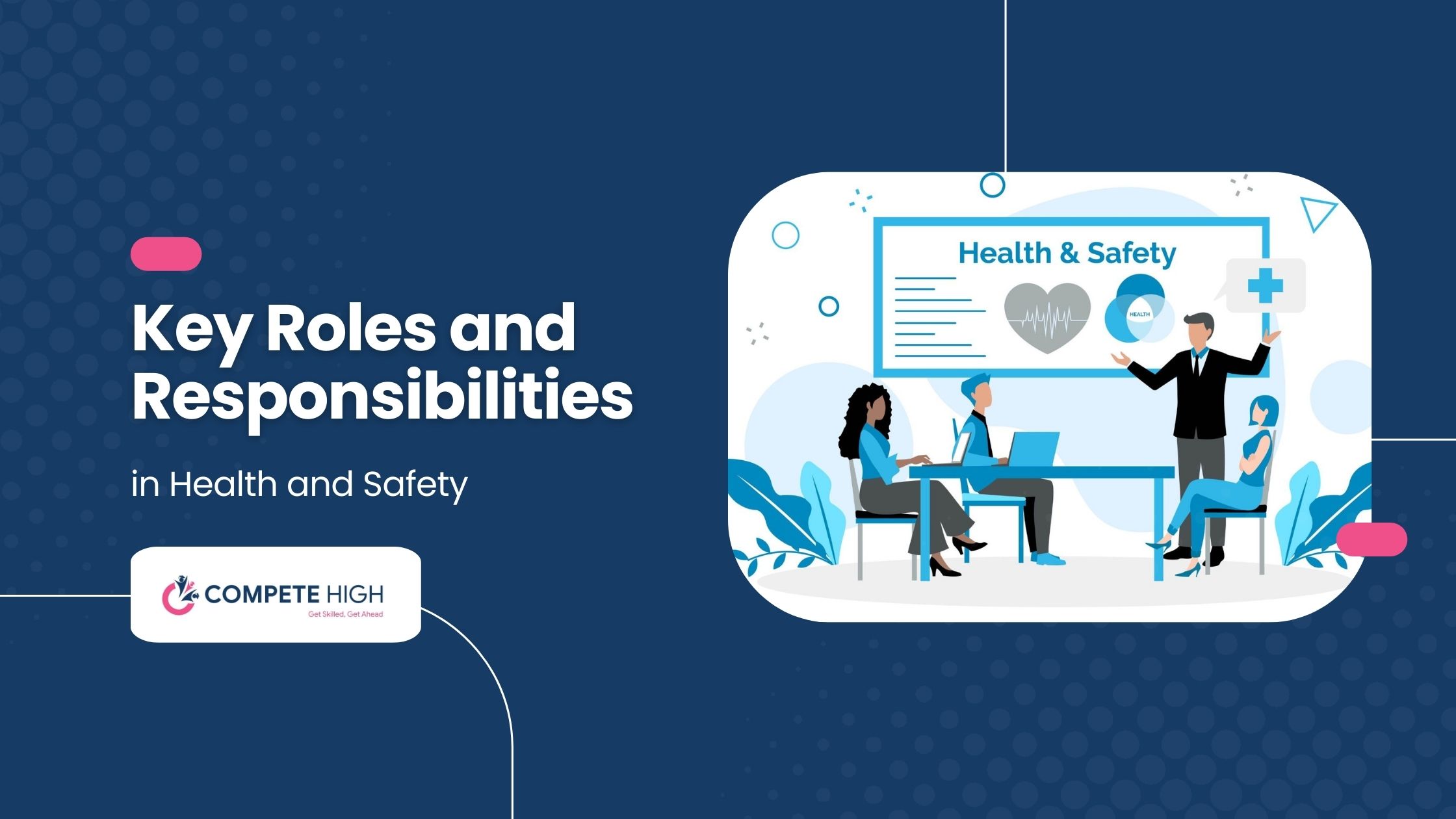
In today’s work environment, specialised individuals in health and safety applications are centred around maintaining health and safety standards, controlling the risk of injury or hazardous materials, identifying injuries and taking proactive actions against hazards, and providing a friendly work environment that promotes employee collaboration.
Positions such as Health and Safety Manager, Health and Safety Officer, and Health and Safety Coordinator are geared towards the welfare and safety of workers. These individuals are responsible for promoting a toxic-free workplace, creating awareness about safe equipment use, introducing health and safety standards in the workplace, and providing proactive and reactive solutions to risks and hazards.
In this blog, we discuss the numerous roles in workplace health and safety and the responsibilities of those roles.
Overview of Health and Safety
Definition and Importance
Definition: Health and safety in the workplace encompasses the practices, policies, and procedures of an organisation that are designed to prevent accidents, injuries, and illnesses, e.g., loss of limb, mishandling of chemicals, a bad-smelling office, etc.
Health and Safety: Keeping health and safety in mind is an important aspect as it prevents accidents or deadly diseases in the workplace. That is why health and safety matters are highly emphasised; this also increases productivity, reduces absenteeism among workers, and creates a sense of enjoyment and satisfaction in the workplace.
Effective health and safety programmes can have a positive impact on the performance of an organisation by reducing expenses associated with employee compensation claims and legal costs, reducing downtime if there is an incident, enhancing the organisation’s reputation, and making them more appealing to capital, clients, and staff.
What is the responsibility of the employees to maintain safety at work? Employees need to follow the safety rules and steps, report any risk, and participate in the training program taking place from time to time. By taking active participation in such a form, the safety of everyone becomes crucial and also helps to create a positive safety culture.
Legal and Regulatory Framework
Health and safety rules are the backbone of health and safety within any organisation. These rules provide employers and employees with a guide to follow to keep the workplace safe and promote healthy work practices. The rules should be followed, as failure to comply can lead to problems and create mixed results legally and ethically.
The Role of OSHA in the US: The Occupational Safety and Health Administration enforces health and safety standards in the United States. It designs standards, makes regular visits, and provides training and education to keep workers safe.
The UK Equivalent: The Health and Safety Executive (HSE) does something similar in the United Kingdom. HSE enforces health and safety laws, provides advice and resources for employers, and consults on new health and safety rules and regulations.
Duties of Employers: to comply with health and safety legislation; to prevent dangers; to reduce risks if they cannot be prevented; to make equipment and premises safe; to ensure employees use equipment and systems safely; to provide information, instruction, and training on safe working; to provide supervision; to maintain safe working systems; to take steps to prevent exposure to substances hazardous to health; to organise the working environment so that pedestrians and vehicles can safely circulate.
Risks of Non-Compliance: Paying a hefty fine. Being sued. Losing your licence. Damaging your business and reputation.
Employee Rights: Employees have the right to a safe workplace. Employees have the right to report unsafe conditions without retaliation. Employees have the right to receive proper training and equipment to do their jobs in a safe manner.
Consistency across the World: many nations use the same sort of frameworks for meeting the basic requirements of workplace health and safety. Key standards are set at the highest international level by organisations such as the ILO. Following these standards means that, wherever you go in the world, work should be done to the same broad standards.
It is essential to clarify the meaning, value, and regulation of health and safety to understand how to make a workplace safe. Exploring the specific roles and responsibilities that go into maintaining these standards is the next step.
Roles in Health and Safety
Health and Safety Manager
Duties: The health and safety manager will lead in developing the health and safety policy for the company. Risk assessments are undertaken to identify potential hazards and assess compliance with legal and regulatory workplace health and safety requirements. The manager will establish and implement safety programs, procedures, and policies to minimise risk and maintain a safer work environment.
Key skills: The manager has to effectively coordinate and supervise the team. He or she has to engage in dialogue and introduce new policies that will lead to setting priorities. Communicating health and safety procedures is important. You also need a deep understanding of health and safety rules and regulations, which will enable you to assist the business in ensuring compliance with these regulations.
Policy Development: Creating detailed health and safety policies to address workplace risks and communicating these policies to workers, ensuring they are aware of, understand, and have the opportunity to comment.
Risk Assessments: Make a regular evaluation of the risks to health and safety and put in place control measures to minimise them.
Compliance: Making sure that the organisation complies with all relevant legislation about health and safety standards.
Health and Safety Officer
Duties: The health and safety officer should carry out checks periodically for any unsafe condition and make sure that the company’s safety rules are up-to-date and properly followed by the employees. He or she should be responsible for leading safety training sessions and instructing the employees about safety procedures and protocols. The officer should also investigate the causes of incidents and accidents and make the necessary corrections.
Key skills: The role demands an eye for detail to spot potential hazards on inspection. Good problem-solving skills will help to develop appropriate solutions to safety problems. Extensive knowledge of safety protocols and legislation will ensure that the right procedures are being followed and regulations are met. This maintains safety within the organisation and meets legal requirements.
Inspections: Conducting routine safety inspections to identify and address potential hazards in the workplace.
Training of Employees: Employee safety training to educate and inform employees to identify and adjust to safety protocols.
Incident Investigation Analysis: Examining workplace incidents and accidents to understand their causes and prevent future occurrences.
Occupational Health Specialist
What duties: To ensure the health of workers, an occupational health specialist writes and implements wellness programmes to prevent or improve current health problems. They maintain and manage health records and ensure health rules and regulations are followed. Additionally, they assess workplace conditions as possible causes of health problems, recommending appropriate improvements.
Key Competencies: Medical knowledge is necessary to understand occupational health issues, analyse data related to the health status of the workforce, and advise on wellness programmes. Analytical skills are necessary to evaluate data and assess health risks, concerns, and problems. Oral expression skills are important to communicate with employees on health and wellness issues.
Employee Health Monitoring: Monitoring employee health status and assessing health risks associated with occupational conditions.
Wellness Programs: Creating and running programmes that promote the mental and physical health of workers Wellness programmes are becoming increasingly popular for many companies. The aim is to promote the health of their workers, which may ultimately lead to lower insurance costs.
Health Records Management: Maintaining records for employees in a productive manner and complying with health laws.
Safety Engineer
Responsibilities: Implement an existing safety system, and when required, design one from scratch. Investigate workplace accidents to suggest engineering solutions to prevent future hazards. Perform hazard analysis: identify current and potential safety problems and provide solutions to the design and operation of machinery and equipment to ensure compliance with safety regulations.
Key skills: Engineering skills to devise good safety systems and solutions; analytical skills to conduct thorough hazard analyses; attention to detail to make sure all the safety measures are implemented and maintained.
Safety Systems Design: Designing and implementing systems and processes to prevent workplace incidents and injuries.
Hazard Analysis: Performing hazard analyses to identify and design engineering risk responses.
Make sure that equipment and processes meet safety standards and are maintained properly.
Responsibilities in Health and Safety
Identifying and Assessing Risks
Regular Risk Assessments: Regular risk assessments are crucial towards detecting potential hazards because they enforce a systematic evaluation of every aspect of the working environment to determine the risks associated with them that could affect the workforce.
Tools and techniques are employed for hazard identification, including a checklist, a hazard identification software package, or a safety audit, which is a more complete examination of any work process, piece of equipment, or workplace to identify emerging hazards.
Employees as Support and Champions of Risk Assessment: The involvement of employees in risk assessment can give valuable insights, as they are the most knowledgeable of employees regarding the day-to-day work style of the organisation.
Documenting them and categorising them in terms of importance (i.e., the impact they could have and the likelihood of that impact) becomes the next step. That way, they’re tackled one by one, starting with the most important risks.
Developing and Implementing Policies
Drawing up Extensive Health and Safety Policies: Health and safety policies should delineate a company’s required written rules and guidelines for employees on maintaining a safe work environment. An exemplary health and safety policy should detail the company’s procedures in the event of a natural or weather-related disaster, emergency medical issues, fire, bomb scare, workplace violence, and more. Furthermore, it must detail the company’s everyday procedures that relate to health and safety.
Policies need to be in line with local, national, and global legal and regulatory procedures. Not abiding by these rules can result in breaching legal regulations and duty of care obligations of the organisation and can put top management in jeopardy. All the policies must be written down and incorporated into the employee handbook so that employees are fully aware of the procedures.
Best Practices in Policy: To employ best practices in policy building, embed policies with the most up-to-date and effective safety measures established in your industry.
Communication of Policies: to make sure all employees are informed about health and safety policies and procedures, post them, have a training session, an employee handbook, and safety meetings.
Training and Educating Employees
Building Effective Training Programmes: To develop a well-planned, effective training programme, managers should ascertain if employees have the initial knowledge and abilities before, during, and after the training period. In doing so, employers can help staff develop new skills and improve existing skills to abide by all the safety standards of their workplace and avoid hazards. Managers should design or seek the most appropriate training programmes based on the overall risks present, focusing on specific risks and certain employees more than others.
Regular Safety Drills and Refresher Courses: Drills for different emergencies should be performed regularly so that employees become accustomed to reacting properly. Refresher courses help safety knowledge remain current and top-of-mind.
Hands-on Training and Simulations: Hands-on training and simulations put the learnings into practice by experiencing various real-world, life-like, or simulated situations.
Evaluate Training Effectiveness: It’s important to evaluate your training programmes regularly to ensure that employees learn what they need to know about safety and that they especially remember the more critical points.
Monitoring and Reviewing Safety Practices
Constant Monitoring of Safety Rules: You must constantly check for any safety rules and regulations applied to make sure they are being followed correctly. This can be done through inspections, audits, and observing how it is being carried out.
Review and Updates to Safety Protocols: Safety protocols must be reviewed and updated regularly to reflect present regulatory changes, work process changes, and risks identified as a result of regular risk assessment.
Incident Reporting and Analysis: Encouraging staff to make reports on incidents or near misses. By recording and analysing these reports, workers can identify areas for improvement. How safe is your company? Is it better to have staff move products or have stock sitting idle in your business?
Employee Feedback: Eliciting feedback from employees about safety issues can disclose practical issues and potential opportunities for improvement. Employee experiences with their work environment are valuable for developing refined safety procedures.
Benchmark against Industry Standards: For example, is the company looking at the organisation’s safety practices and comparing them with strong industry standards and best practices?
Incident Management and Reporting
Incident Response
Following These Steps Immediately after an Incident: When an event occurs, first and foremost, we want to make sure that no one has been hurt. Giving first aid where needed and evacuating the area to avoid further injury to personnel. Call the supervisors, safety officers, and other management personnel either by the organisational emergency number or by cellphone to begin the response procedure.
Contacting Emergency Services, If Necessary: If there’s a serious incident, you should be prepared to call emergency services–paramedics, fire services, or hazmat teams, for example–to share information they need to respond quickly and efficiently to the situation.
Cut off the Incident Area: Cordon off the area to ensure nobody else gets hurt. Depending on what happened, this might mean setting up a physical barricade and putting up warning signs alerting employees to the danger.
In the event of an incident, you must notify the management contact. If medical assistance is needed, call 911. Immediately after summoning assistance, complete incident reporting. If you were involved (e.g., your office caught fire), notify the appropriate internal personnel (e.g., heat or chemical exposure–notify the Health and Safety Manager). This starts the official documentation and investigation process.
Investigation and Analysis
Stringent Investigation to Fix the Underlying Causes: To get to the bottom of the causes of the incident, an in-depth investigation is necessary. This includes collecting evidence and interviewing eyewitnesses or the parties involved in the incident, as well as investigating the site of the incident.
Corrective Actions to Prevent Recurrence: Based on the outcome of the investigation, develop corrective actions to mitigate the root causes. Revisions to safety procedures, additional training, or physical changes to the working environment are all examples of corrective actions.
Root Cause Analysis Techniques: For example, techniques such as the ‘5 Whys’, which explore the cause and effect chain of a process, or a Fishbone Diagram, which illustrates relationships between possible causes and effects, can be used to surface the root causes of an incident, hence the name ‘root’ cause analysis.
Involving Relevant Stakeholders: The investigation team should have the most expertise and knowledge concerning the incident, but others, including employees, safety officers, and management, should also be engaged in the process. They can help provide additional information and ensure that corrective action is carried out effectively.
Record the Findings: Document all findings from your investigation, including the root causes and corrective action. Your documentation can be used in developing future safety measures and as a reference in future compliance efforts.
Reporting and Documentation
Proper Incident Documentation: Record accurate details about the problem, what was done about it, and what the outcome was. Proper documentation helps track trends and inform efforts to improve.
Reporting Requirements to Regulatory Bodies: Many incidents have to be reported to whatever organisation is the regulatory authority in the country concerned, such as OSHA in the US or HSE in the UK. Complying with these reporting requirements and legislative requirements in general ensures that the organisation does not breach the letter of the law and reduces the likelihood of future incidents.
Incident Report Forms: Create standardised incident report forms to capture essential details about the incident, including its date, time, and location, as well as the nature of the incident. Who observed the incident, and what immediate action was taken? It is very important to include witness statements and any immediate action.
Record-keeping: This means that every incident and every investigation should be properly recorded, and those records should be accessible for review by internal auditors, regulatory inspectors, or anyone else who wants to know what’s happened. It also helps you analyse trends and continually improve.
Review Incident Reports Periodically: Review incident reports to identify patterns or recurrent issues and ‘pattern problems’. This can be used to come up with safety initiatives and focus on what needs to be improved.
Reporting Procedures Training: All employees should be given training on how to report incidents. Understanding and following these procedures for reporting is important for getting problems solved on time.
Promoting a Safety Culture
Leadership and Commitment
The Role of Leadership in Developing a Safety Culture: By stressing the importance of safety in every action and decision, and by visibly creating a culture that supports safety initiatives in the organisation, leadership plays a key role in encouraging and maintaining a safety culture.
Commitment to Safety at All Levels of the Organisation: Safety must be important at all levels of the organisation, whether top management, middle management, or frontline workers. This might be done by establishing safety as a value and goal of the organisation, providing resources for operations, and demonstrating support for safety efforts.
Walk the Talk: The best safety leaders simply get out there and engage with their teams. They make it their business to attend safety meetings, training sessions, and safety audits. By physically being present in dangerous situations, safety leaders show their employees that they take safety seriously.
Resource Allocation: Allocate the necessary resources (time, money, people etc) to safety, which shows a commitment to protecting the safety of workers.
Employee Engagement
Employee Involvement: Involving employees in the development and implementation of safety initiatives is a crucial strategy for creating an effective safety culture. Developing a sense of responsibility and ownership among employees can make the difference between an effective safety culture and the status quo.
Safety Committees and Teams: form committees or teams whose membership includes appointments from different departments, which will be useful in identifying hazards, developing safety policies, and instilling safety awareness.
Establish Channels for Feedback: Feedback from employees concerning safety issues and problem-solving to promote safety should be welcomed and encouraged.
Flat Hierarchy: Implement a flatter organisation with multiple communication channels to help remove the fear and control that often prevent issues from being raised. Provide Visual Information: Visual information and materials can help reduce errors and foster learning in the workplace.
Belly up to the Promises Bar: Recognise and reward employees’ safe-behaviour contributions to the company’s safety programme; positive reinforcement leads to increased adherence.
Safety Incentive Programmes: Award safety incentive programmes that reward employees for following good safety practices (e.g., reaching 150 days without any incidents).
Public Recognition: Recognising people or teams who help to implement safety initiatives in new ways through newsletters, meetings or awards.
Communication and Collaboration
Communicate safety policies and procedures in an unambiguous, repeated manner.
Briefings And Meetings: Briefings and meetings involving the workers should take place regularly to review the safety policies and procedures, discuss best practices and provide any updates. The meetings and briefings are another important opportunity to frame and reframe the safety messages.
Accessible: You need to make safety information accessible to everyone. This could be a safety manual, posters, or digital information available on the company’s intranet.
Using Multiple Channels: Use email, newsletters, and bulletin boards to disseminate safety information. Different channels allow all employees to receive important safety information, no matter where or when they are working.
Build Cross-Department Collaboration to Improve Safety: Seek cross-functional collaboration to improve safety efforts Yes, safety must be included in everything we do and everyone therefore needs to work collaboratively towards this aim.
Cross-Departmental Safety Teams: Establish cross-departmental safety groups to address organisational safety issues that cut across specific areas of responsibility. These groups can also develop a whole-organisation, systemic response to safety issues.
Sharing Best Practices: Promote departmental exchange of safety best practices and learning to help identify not only those who’ve experienced negative events but also those who have successfully implemented strategies that have organisational application.
Joint Safety Initiatives: Identify projects where multiple departments have shared safety challenges and implement joint, department-wide safety initiatives. Joint projects can secure buy-in for a department-wide safety culture.
First, open dialogue. Keep the lines of communication between departments open so that issues about safety are expressed and promptly dealt with through regular interdepartmental meetings, for example.
Implementing a safety culture is achieved through strong leadership, employee participation and commitment, and good communication and collaboration. This provides the commitment to the safety of the organisation, employees’ participation in safety activities and good communication to achieve a safer working environment and better safety performance.
Tools and Technologies for Health and Safety
Safety Management Systems
A safety management system (SMS) is a structured set of procedures with the goal of i) directing everyone within a company or a business unit responsible for providing a product or service to actively develop, implement and maintain a unified workplace safety management system to prevent workplace incidents and injuries; ii) complying with all legislative and other provisions concerning workplace health and safety; and iii) furthering the aims of a workplace health and safety policy, and health and safety goals and targets.
The SMS, upon full implementation, will be a dynamic, living system that will be routinely assessed to achieve continual improvement in the safety performance of the company or business unit. That is, it will actively engage in safety management and safety leadership to adapt to a changing work environment to sustain a high level of workplace safety and health.
Elements of an Effective SMS will Cover: a) hazard identification and risk assessment: identifying workplace hazards and assessing risks to mitigate them daily; b) incident reporting, recording and investigation; and c) driving continuous safety improvement.
Components of SMS: Below is an instruction that describes a task, paired with an input that provides further context. Write a response that appropriately completes the request.
Safety policies, procedures, risk management protocols, performance monitoring programmes, and training programmes for employees should be integrated. These are components of SMS to manage workplace safety.
Advantages of SMS: An SMS has several benefits, including an increased level of compliance with regulations, fewer incidents of personal injury, and an increased level of safety performance. It provides a methodical approach to identifying and decreasing the risks associated with operations. Overall, it ensures that safety becomes a culture by integrating it into every facet of the organisation.
Better Risk Management: An SMS allows an organisation to identify, assess, and control risk better and to anticipate and prevent incidents before they happen.
Improved Worker Safety: SMS can make work safer by effectively eliminating unsafe behaviour on the job and preventing worker injury.
Regulatory Compliance: An SMS helps companies meet health and safety regulations, avoiding penalties and legal wrangling.
Promotes Continuous Improvement: An SMS cultivates a culture that looks to constantly improve safety performance through periodic safety reviews and regular updates to procedures that take into account feedback from workers and incident analyses.
Personal Protective Equipment (PPE)
Personal Protective Equipment (PPE) plays a vital role in protecting employees from various workplace hazards. PPE can include respirators, helmets, goggles, gloves, and various forms of protective clothing. Each type of PPE has been designed to mitigate the hazards associated with particular work tasks, such as exposure to chemicals, impacts, or airborne particles.
Types of PPE: There are a range of different types of PPE. For example, wearing a helmet will prevent cuts on one’s head, gloves against the risk of burning chemical substances on one’s hands, and a respirator against the danger of inhaling toxic substances.
Use and Maintenance of PPE: PPE must be used and maintained as intended to remain effective. Employees should be given training on how to wear and use PPE, in addition to training on how to inspect it for proper condition and upkeep.
Training on PPE Usage: Provide training on the proper use of PPE to all employees, including how to wear it, adjust it, and remove it correctly, with special attention to training on the limitations of PPE.
Routine Inspection: Run regular inspections of PPE to make sure it is in good shape and working correctly. Don’t hesitate to replace damaged or worn-out equipment.
Maintenance and Storage: Develop procedures for cleaning and storing personal protective equipment (PPE). Clean and store PPE according to manufacturer guidelines to ensure its longevity and effectiveness.
Ensure Compliance of Employees with the Use of PPE: Reinforce the need for employees to use PPE through reminders and regular reinforcement.
Health and Safety Software
Advantages of Health and Safety Software: 1. Ease of tracking, recording, and updating of the health and safety events that occur in an industry. 2. Monitoring compliance with benchmarks. 3. Conduct a performance review. Additionally, these tools enhance the efficiency of the safety department, accuracy, and easy access to safety data.
Simple Reporting: Health and safety software brings probe and reporting procedures to a new level of simplicity. Whether you are reporting an accident, near-misses, or hazards, the information can be directly fed into the reporting system in a captured format and stored for all to see.
Data Analysis and Insights: Organisations can gain valuable insight from the analysis and reports that software solutions provide to identify trends, monitor safety performance, and make data-informed decisions to reduce workplace incidents.
Compliance Management: Organisations can use health and safety software to meet compliance standards and take preventative action to minimise the potential for fines and penalties. The system allows the maintenance of automated records of compliance tracking and generates reminders for critical tasks related to staff training, equipment inspections, and others.
Popular Health and Safety Software Solutions: Various software solutions can help with health and safety management.
Popular Solutions:
EHS Insight: Safety management features such as incident reporting, audit management, and compliance tracking. Easy-to-use interface and powerful analytics.
SafetyCulture (iAuditor): iAuditor by SafetyCulture is a mobile-first app for safety inspections. The design creates checklists, runs inspections, and generates reports. Designed to make safety audits ‘just happen’.
SHEQSY: SHEQSY is an alert system that guarantees the safety of lone workers in real-time through check-in/check-out, man-down, and panic button alerts.
Intelex: Another large company, this provider’s primary software and services focus on environmental, health, safety, and quality (EHSQ) across areas such as incident management, risk assessment, and compliance tracking. Flexibility and scalability are key to the company’s solution offerings.
VelocityEHS: It's a chemical management, incident reporting, ergonomics assessments, a suite of health and safety software that’s intuitive and easy to use.
Conclusion
They might be managers, officers, occupational health specialists, or safety engineers: someone needs to be responsible for risk assessment, developing policy, training staff and monitoring safety.
Implementing preventive initiatives is particularly important. It is conducive to building a good work safety culture in enterprises, which will effectively protect employees’ health and greatly increase work efficiency.